Environmental criteria
IMPORTANT INFORMATION FOR OUR SUPPLIERS
We are currently in the process of implementing an environmental management system in compliance with ISO 14001:2015.
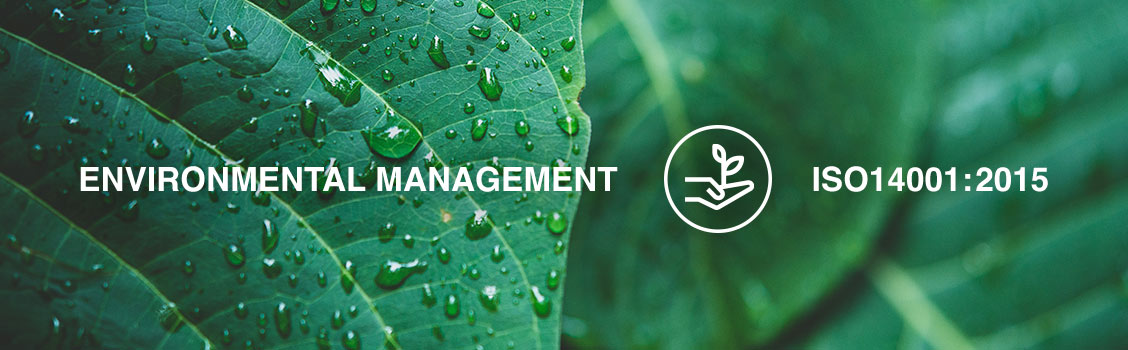
What is an environmental management system?
An environmental management system is a tool to minimize our impact on the environment. It encompasses not only our own activities, but also those of the suppliers who provide us with the materials, products and services we need.
In this regard, as a RAYPA supplier, it is essential that you comply with the following requirements related to environmental management:
– Comply with all applicable environmental legislation.
– Proper management of waste and emissions generated.
– Adopt sustainable resource consumption practices..
ATTENTION
If you have an environmental management certificate, please reach out to us to send us the certificate (ISO-14001, etc.) by e-mail.